Understanding the Significance of Plastics Injection Mold in Today’s Manufacturing Landscape
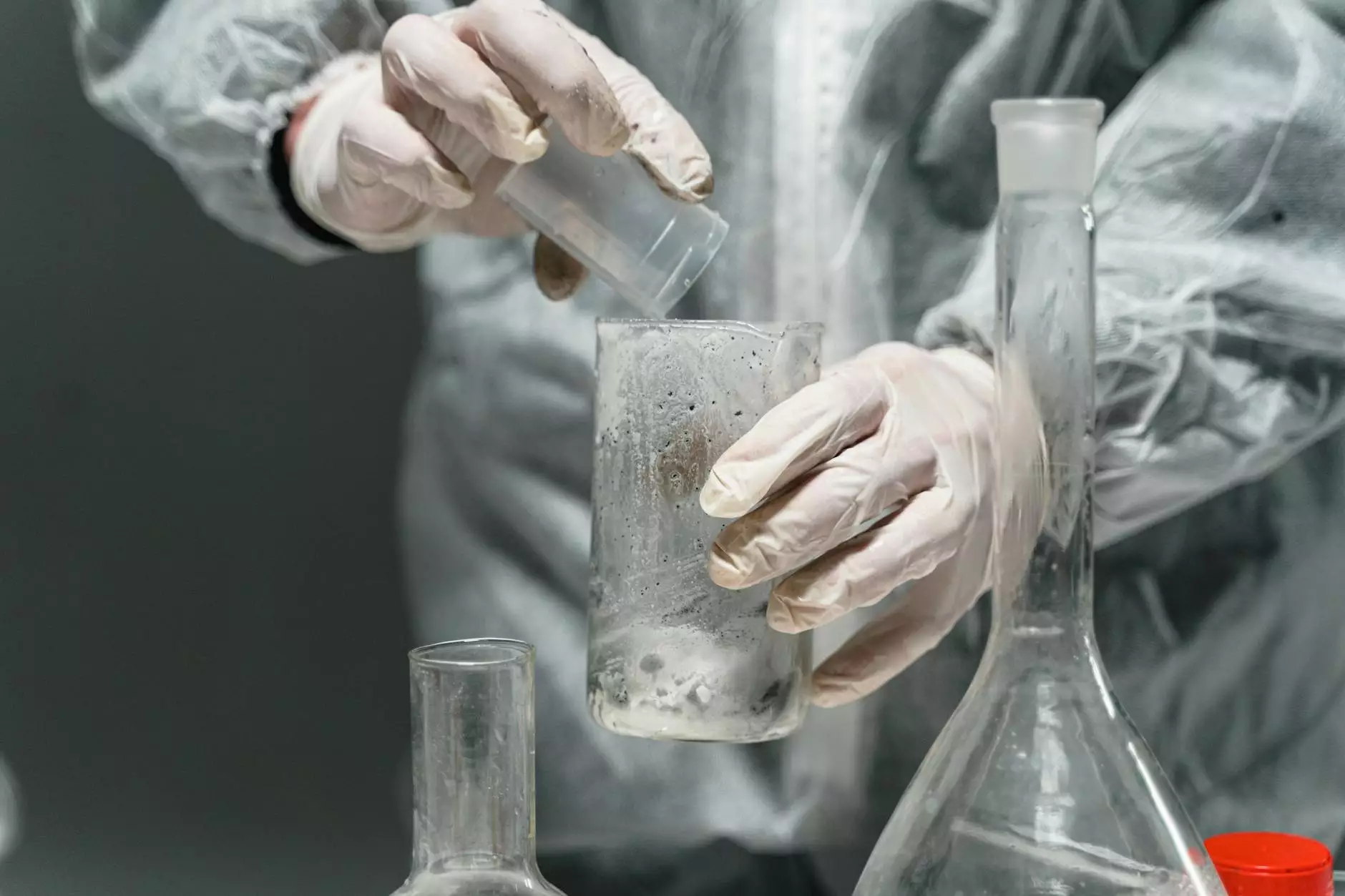
The world of manufacturing has witnessed remarkable advancements over the past few decades, with plastics injection mold technology leading the charge in revolutionizing production processes. As industries continue to evolve, the ability to produce complex shapes and components with precision has become increasingly crucial. This article delves into the intricacies of plastics injection mold, its applications, benefits, and how businesses like deepmould.net are at the forefront of this transformative process.
The Mechanics Behind Plastics Injection Mold
At its core, plastics injection molding is a manufacturing process that involves the creation of parts by injecting molten material into a mold. This method allows for high production rates and the ability to create intricate and detailed parts consistently. The process can be broken down into several key stages:
- Granule Preparation: The process begins with the preparation of plastic granules, which are the raw materials used for molding.
- Heating and Injection: The granules are fed into a heated barrel where they melt into a viscous liquid, which is then injected under pressure into a pre-designed mold.
- Cooling: Once the material fills the mold, it is allowed to cool and solidify, taking on the shape of the mold.
- Demolding: After cooling, the mold is opened, and the newly formed part is ejected. Depending on the complexity, this may require assistance from ejector pins or plates.
- Finishing: The final stage may involve additional processes such as trimming, painting, or assembling, depending on the specific requirements.
Applications of Plastics Injection Mold
The versatility of plastics injection mold is evident in its wide-ranging applications across numerous industries:
- Automotive Industry: From dashboards to battery casings, plastics injection molding plays a vital role in producing lightweight, durable components.
- Consumer Goods: Everyday items such as containers, household appliances, and toys are commonly manufactured using this process due to its efficiency and cost-effectiveness.
- Electronics: The precise molding of components such as connectors, switches, and casings makes it indispensable in the electronics sector.
- Medical Devices: In an industry governed by strict standards, the ability to produce sterile and complex shapes is a major benefit of plastics injection mold.
- Packaging: The production of custom packaging solutions that are lightweight yet strong is another significant application in this field.
The Advantages of Using Plastics Injection Mold
Investing in plastics injection mold technology offers numerous advantages that can enhance production capabilities:
- Cost Efficiency: Once the initial mold is created, the cost per unit decreases significantly, making it economically viable for mass production.
- Speed: The process can produce thousands of units in a short timeframe, reducing lead times and meeting consumer demands efficiently.
- Precision: Molding technology allows for tight tolerances and complex designs, often eliminating the need for secondary processing.
- Material Versatility: Various thermoplastics and thermosetting polymers can be used, allowing manufacturers to select materials based on specific performance requirements.
- Reduced Waste: The process is highly efficient with minimal waste generated, contributing to more sustainable manufacturing practices.
Overcoming Challenges in Plastics Injection Mold
Despite its significant benefits, plastics injection mold also comes with challenges that must be navigated:
- High Initial Costs: The design and manufacturing of molds can be expensive, making it a barrier for small-scale projects.
- Complexity in Design: Creating the mold requires skilled engineers to ensure that the design meets production requirements without flaws.
- Material Limitations: Not all materials are suitable for injection molding, which may limit the production options for certain applications.
- Maintenance of Molds: Regular maintenance is necessary to prevent wear and prolong the mold’s life, which adds ongoing costs.
Deep Mould: Leading the Way in Plastics Injection Mold Technology
As a prominent player in the field of plastics injection mold, deepmould.net exemplifies innovation and precision in manufacturing. With a commitment to quality and customer satisfaction, deepmould.net has established itself as an industry leader that caters to a diverse clientele across various sectors. Here are some reasons why deepmould.net stands out:
Expertise and Experience
With decades of experience in plastics injection molding, the team at deepmould.net possesses the knowledge and skills necessary to tackle the most complex projects.
State-of-the-Art Technology
Deep Mould utilizes the latest advancements in molding technology, ensuring that clients receive high-quality products that meet even the most stringent standards.
Custom Solutions
Understanding that every client has unique needs, deepmould.net specializes in providing custom molding solutions tailored to specific requirements, enhancing both functionality and aesthetic appeal.
Sustainable Practices
Being environmentally conscious, deepmould.net prioritizes sustainable practices within its manufacturing processes by reducing waste and utilizing recyclable materials wherever possible.
Future Trends in Plastics Injection Mold
As industries evolve, several trends are shaping the future of plastics injection mold technology:
- Smart Manufacturing: Integration of IoT and AI technologies is expected to enhance efficiency and provide real-time data analytics to improve production workflows.
- Advanced Materials: The development of new, high-performance materials such as bioplastics and composites is expanding the applications of injection molding.
- 3D Printing Synergy: The combination of traditional injection molding with additive manufacturing technologies may lead to new possibilities in design and prototyping.
- Increased Sustainability: As environmental regulations tighten, there will be a continued focus on reducing carbon footprints through eco-friendly practices in molding.
Conclusion
In conclusion, the role of plastics injection mold in modern manufacturing environments cannot be overstated. Its ability to produce high-quality, complex components efficiently makes it indispensable across various industries. Companies like deepmould.net are setting standards for excellence and innovation within this space, ensuring that businesses can meet the demands of a fast-paced market. As technology continues to advance, the future of plastics injection molding looks promising, heralding new opportunities for manufacturers and consumers alike.