Understanding Final Drives for Mini Excavators
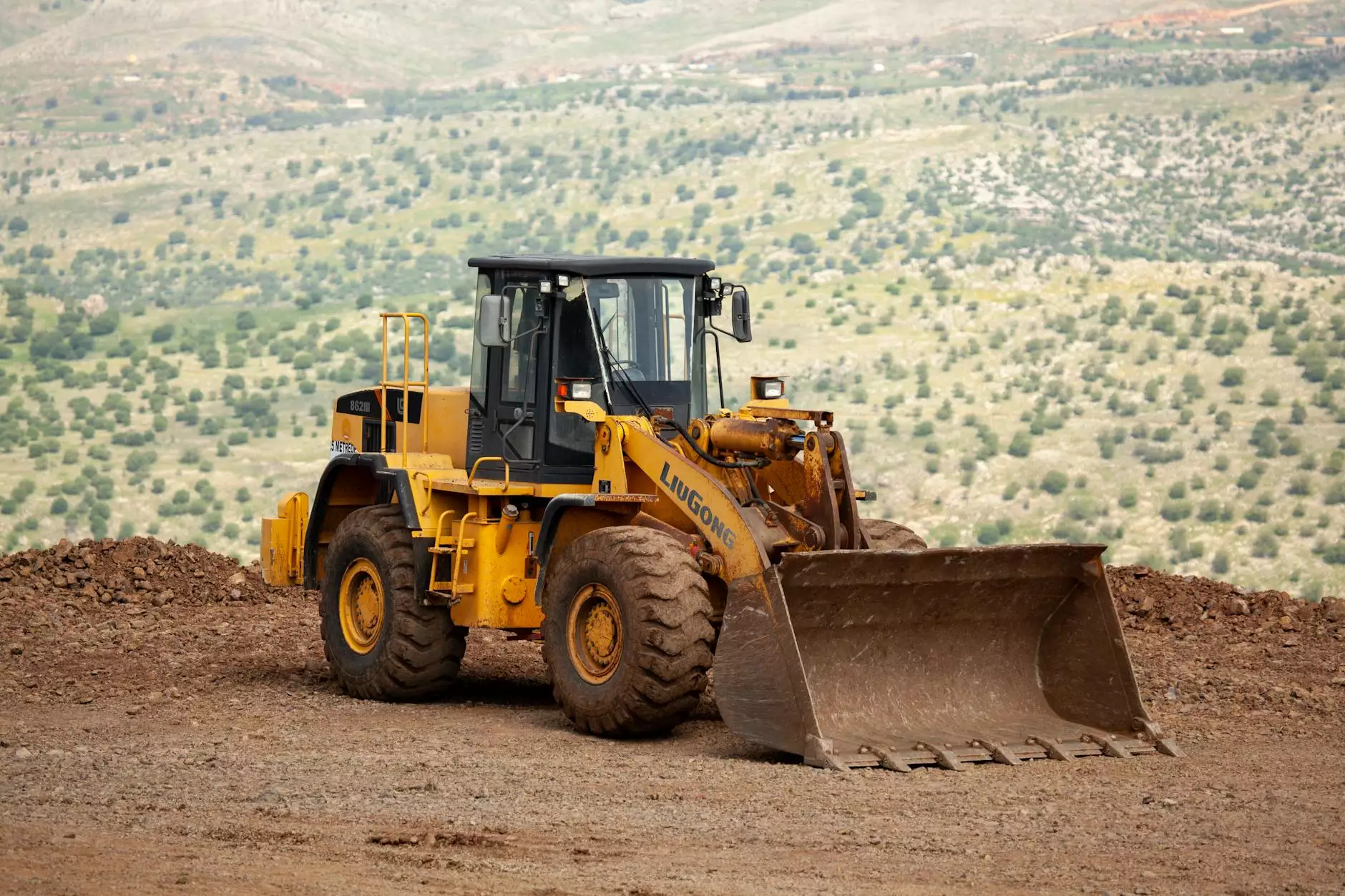
Final drives for mini excavators are crucial components that ensure the smooth operation of these versatile machines. As the construction industry continues to evolve, understanding these components can significantly impact productivity, maintenance costs, and machine longevity. In this article, we delve into the intricacies of final drives, exploring their functionality, benefits, and the crucial role they play in the overall performance of mini excavators.
What are Final Drives?
Final drives are mechanical assemblies that transfer power from the engine and transmission of a mini excavator to the tracks or wheels. This transfer of power enables the excavator to move and operate heavy equipment with precision. A final drive typically includes several components: a drive motor, gear reduction, and output drive mechanism. It is imperative to understand that the efficiency of these components directly influences the performance of mini excavators.
The Anatomy of Final Drives
To appreciate the functionality of final drives, let's examine their main components:
- Drive Motor: This is typically a hydraulic motor that provides the necessary power for movement.
- Gear Reduction: A system of gears that decreases the speed and increases the torque delivered to the tracks or wheels, maximizing the equipment's lifting and digging capabilities.
- Output Drive Shaft: Transfers the rotational energy from the motor through the gear system to the tracks or wheels.
- Housing: Encloses all components and protects them from debris and environmental factors.
How Final Drives Work
Final drives for mini excavators work on a simple principle: power transfer. Here's a high-level breakdown of the process:
- The engine generates power, which is routed to the hydraulic system.
- The hydraulic motor receives this power, where it converts hydraulic energy into mechanical energy.
- This mechanical energy is then transmitted through the gear reduction system, where the speed is reduced while torque is increased.
- Finally, the output shaft rotates, propelling the tracks or wheels forward or backward.
Types of Final Drives
There are various types of final drives suited for different applications and excavator models:
1. Planetary Final Drives
These are the most common type of final drives used in mini excavators. They feature a planetary gear system that allows for efficient power distribution and compact design. The benefits of planetary final drives include high torque capacity and improved durability.
2. Spur Gear Final Drives
These are simpler in design and typically found in smaller machines. They use straight-cut gears to transmit power. Although they can be less durable than planetary systems, they are often easier to manufacture and maintain.
Benefits of High-Quality Final Drives
Investing in high-quality final drives for mini excavators brings several benefits:
- Enhanced Efficiency: Superior final drives provide better energy conversion, ensuring that more power reaches the tracks or wheels.
- Increased Durability: High-quality materials and construction result in longer-lasting components that reduce the frequency of repairs and replacements.
- Improved Performance: Well-engineered final drives enhance operational performance, allowing for smoother rides and quicker responses in various terrains.
- Reduced Maintenance Costs: Investing in durable final drives helps minimize downtime and maintenance expenses over the machine's lifespan.
Signs of Final Drive Wear
It's essential to monitor the condition of your mini excavator's final drives, as wear and tear can lead to significant issues. Look for these signs:
- Unusual Noises: Grinding or clunking sounds when operating the excavator may indicate issues with the gears or bearings.
- Loss of Power: If the machine struggles to move or perform tasks, the final drive could be malfunctioning.
- Fluid Leaks: Any fluid leakage around the final drive area is a cause for concern.
- Vibration: Excessive vibration when operating can signal misalignment or internal damage.
Maintenance Tips for Final Drives
Proper maintenance of final drives can prolong their lifespan and improve performance. Here are some tips to ensure your mini excavator's final drives remain in top condition:
- Regular Inspections: Frequently inspect the final drives for signs of wear, leaks, or damage.
- Change Fluids: Adhere to fluid change intervals as recommended by the manufacturer to ensure optimal lubrication.
- Inspect Bearings and Seals: Check the bearings and seals for wear and replace them as necessary to prevent contamination.
- Monitor Hydraulics: Keep the hydraulic system maintained and functioning correctly to prevent excess strain on the final drive.
Choosing the Right Final Drive for Your Mini Excavator
When selecting a final drive for your mini excavator, consider the following factors:
- Compatibility: Ensure the final drive is compatible with your specific model of mini excavator.
- Performance Requirements: Assess the performance needs of your projects to choose a final drive with the appropriate torque and speed ratings.
- Quality and Brand Reputation: Invest in products from reputable manufacturers known for their durability and performance standards.
- Cost vs. Value: Balance the initial cost with the long-term benefits of reduced maintenance and downtime by choosing high-quality options.
Where to Buy Final Drives for Mini Excavators
If you are in need of final drives for mini excavators, consider reputable suppliers like Shop Hydraulic America. Their inventory includes a wide range of auto parts and supplies specifically designed for optimal performance in heavy machinery.
Conclusion
Understanding final drives for mini excavators is crucial for anyone involved in the construction and heavy machinery industries. By grasping their operation, maintenance, and selection criteria, you can significantly enhance the reliability and efficiency of your mini excavator. High-quality final drives not only improve performance but also reduce maintenance costs and downtime, proving to be a wise investment for any business owner or contractor.
As you venture into the world of excavators, remember that the right knowledge and equipment can set you apart in a competitive landscape. Choose wisely, maintain diligently, and reap the benefits for years to come.